Wrapping line lifts hygiene for antibiotics test kit
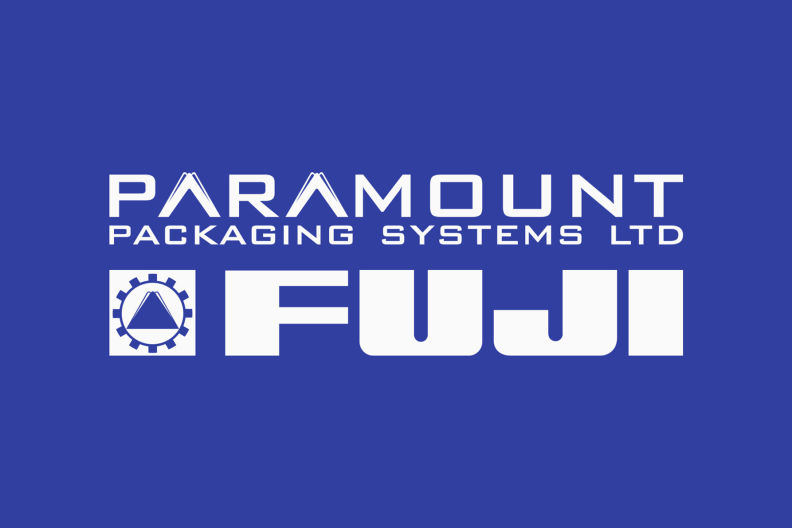
Trek Diagnostic Systems, East Grinstead, has reduced the labour cost for packing trays of antibiotics used in laboratory diagnostic tests, eliminated repetitive manual work and improved cleanliness, following the installation of a purpose built flow-wrapping line supplied by Paramount Packaging Systems.
The new line brings together a number of once separate packing operations and, with the tray now handled upside down under filtered air, has also eliminated the need for aluminium foil lids to guard against entry of dust prior to wrapping.
Trek supplies its Sensititre brand trays to medical and veterinary laboratories, where they are used with patient samples to determine the most effective antibiotic to counter an infection. The 150 x 100mm trays, each with 96 ‘wells’ carrying a different antibiotic, are classed as clean products, rather than sterile.
“Previously a considerable amount of handwork was involved, loading and unloading the trays between the dryer, labelling, addition of desiccant and flow-wrapping,” explains Darren Frost, production manager at Trek. “Now the line is automated, with minimal handling of the product, the risk of contamination is reduced and the aluminium lid is no longer necessary.” After filling and drying, trays are loaded manually onto the in-feed of the packing line, where they are inverted by a belt conveyor system and directed base-up into the flights of the main conveyor. The entire line, 10 metres long, is covered by perspex guarding under which microbiologically filtered air is introduced to provide gentle air movement and prevent entry of dust.
The first operation is print-apply labelling, to identify each tray along its side with a bar code which includes lot number, expiry date and product code. Label presence and code is verified automatically by a scanner linked to a reject system which, for fail-safe security, rejects every tray unless a positive accept signal is received.
Next, a desiccant sachet is cut from a reel and automatically placed on the tray, its presence checked by a photo-cell. Wrapping then takes place on a Fuji Alpha 5 FW3400 BSB machine. This is a bottom reel flow-wrapper, with the film unwinding onto the bed of the machine, allowing the trays to be handled upside down yet with the longitudinal seal at the base. Sealing jaws move in a box motion, following the film, to provide the extra dwell time necessary for secure, hermetic seals on the high barrier aluminium foil/polyethene laminate employed by Trek. Line speed is 40 trays a minute.
“Reduced risk of contamination is a key advantage of the line,” points out Darren Frost. “However a further benefit is that highly repetitive work has been eliminated, along with the potential for repetitive strain injury.”