What are the different types of flow wrappers and their benefits?
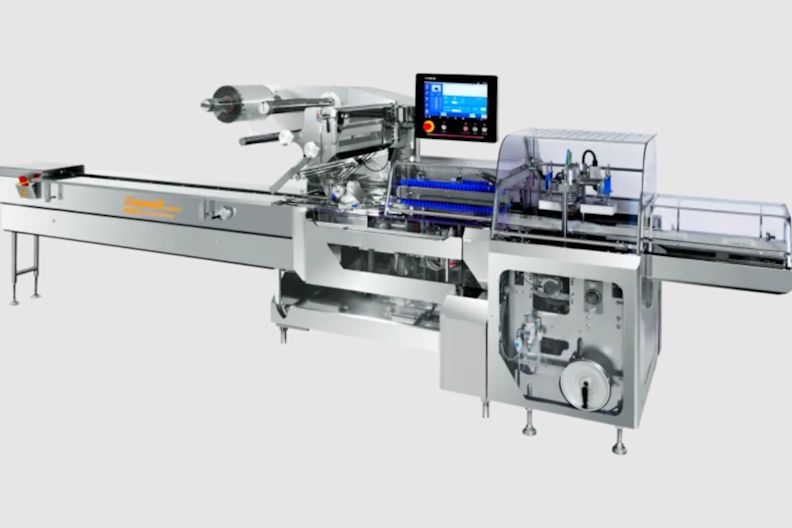
Flow wrappers, also known as horizontal form-fill-seal (HFFS) machines, are widely used in multiple industries to wrap products in a flexible film. These versatile machines offer various benefits such as adding protection to products, increasing shelf life, speed, efficiency and versatility, making them an essential component of modern packaging lines.
In this article, we will explore the different types of flow wrappers and their specific advantages.
Firstly, what is a horizontal flow wrapper?
A Horizontal flow wrapper takes a product from the infeed conveyor of the wrapper, packaging film on a roll is formed into a tube by the forming box, sealed longitudinally by the fin sealers, the product is placed inside the film tube and the end seal cuts and seals the product in an individual pack. This all happens in one fluid movement hence the process being called form fill and seal. There are a number of models of flow wrapper, not just varying in size but in the way the film is fed into the machine and the pack produced. The selection of the correct wrapper for an application depends on the product to be packed and pack required.
Their benefits include:
- Versatility: they can handle a wide range of product sizes and shapes, making them suitable for diverse packaging needs and multiple industries from Food to Pharmaceutical.
- Efficiency: flow wrappers operate at various speeds depending on the application and can run from 2 packs per minute up to 2000 packs per minute.
- When equipped with optional devices like infeed systems and auto splice units, it ensures a continuous supply of packaging material to the flow wrapper. With these additions there will be no stoppages or the need to reject packs that don't meet the specifications, instead you will have an efficient, consistent and dependable system.
Film from above wrappers
Film from above wrappers are the most common type of flow wrappers and as the name suggests the film enters the wrapper from above, with the fin of longitudinal seal made beneath the product and the end seal jaws in rotary or box motion.
Products such as chocolate bars, bread rolls, wet wipes, blister packs of tablets and trayed products are all easily handled on a film from above flow wrapper.
Inverted or back seal wrappers
Inverted or back seal wrappers have the advantage of the film entering from below, so the product is placed directly onto the film. This works especially well for grouped items, such as bread sticks, fresh sausages, bunches of herbs and IV bags. Heavy and sticky products, for instance blocks of cheese, pastry or tortillas, are also handled easily on an inverted wrapper, as the products are carried through the wrapping process in the film and supported underneath by a conveyor.
Three-side seal wrappers
The three-side seal horizontal wrapper is commonly used for packaging small, flat, or regular-shaped products that require individual packaging. It provides a visually appealing presentation and the sealed packages can be easily stacked or displayed. Overall, the three-side seal horizontal wrapper is a versatile packaging solution that offers efficient and reliable packaging for various products. The benefits of three-side seal wrappers include:
- Simplified sealing process compared to four-side seal wrapper.
- Single web of material used.
- Easy open and re-closable functions can be easily included using a peelable material and reclose label.
- Portability: The compact size of sachets makes them convenient for on-the-go consumption portion packs.
- Easy open functionality can be easily added to the pack using a zip or slit and tape.
Four-side seal wrappers
Four-side seal wrappers are used to create a flat flexible pack with all four sides sealed. These wrappers are commonly employed in packaging products, such medical devices, wound dressings, sliced meat and cheese.
The benefits of four-side seal wrappers include:
- Unobstructed product visibility: This is achieved by producing the packs using two webs of material to create a clear top web display.
- Sterilisation: In the case of medical dressings, the permeable top layer will allow a chemical sterilisation agent to enter and sterilise the product within.
- Portability: The compact size of sachets makes them convenient for on-the-go consumption or single-use purposes.
- Product protection: The tight seals formed by four-side seal wrappers help preserve product freshness and prevent leakage or contamination.
- Easy open functionality can be easily added to the pack using a peelable material, easy open reclose label or a seal strip.
All versions of flow wrappers play a crucial role in the packaging industry by providing an efficient packaging solution that minimises the amount of packing materials required, whilst ensuring product presentation, protection, increasing shelf life and an easy to open pack. By understanding the different types of flow wrappers and their advantages, businesses can select the most suitable option to meet their packaging needs efficiently and effectively.
If you have any questions about the different types of flow wrappers and their benefits, we’re happy to help! Contact Paramount Packaging Systems on 01252 815 252 or fuji@paramount-packaging.co.uk